EXTENSION SPRINGS
This section will tell you how to make extension springs.
(For how to make extended hooks, see the torsion spring page.)
Once you have your setup done, the first thing you should do is make sure you have enough wire.
Wire Length
If you're using light wire, or if you're making short extension springs with wire up to about .250", you really don't need to know how much wire you need for each spring - just be sure you have more than enough. You can figure a rough length by taking the length of the body of the spring, dividing by the wire size (which gives you an approximate count of the number of coils in the spring) and then multiplying that by 3.3. It'll probably come out too long, but that's okay - you can use your first couple of springs to set up for making your loops.
If you want to make long extension springs out of wire over about .250" or if you want more than 50 of one design, I recommend that you go to a spring shop and have them make your springs for you.
Coiling the First Trial
Now let's make a spring.
Cut yourself a piece of wire that's the right length. If you're using light wire, you can just undo the wire and let it sit on the floor in front of the lathe or winding machine. Take the end of the wire on the inside of the coil for your starting end - that way it won't tangle. If you're coiling short springs, cut yourself off a LONG length of wire, so you can coil several springs at the same time. Be sure that anyone else in the area stays out of danger while you do the rest of this. Also, get your oven fired up.
Put the wire into your setup and move your wire guide to the left, close to where the pickup pin is. As you look down at your setup, it should look like this (these diagrams will show both a hand-held wire guide and a tool post-mounted wire guide):
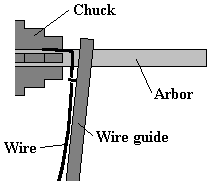
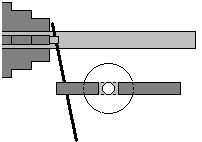
Start your coiling. Move the chuck DEAD SLOW until you're sure that the wire is seated on the pickup pin and the pin on your wire guide. Let a couple of coils lay down on the arbor.
READ THE NEXT STEP ALL THE WAY THROUGH BEFORE YOU START IT.
When you have your first coils laid down on the arbor, you'll then need to do two things at the same time.
First, bring the wire guide a little to the left. You want there to be a gap between the first two coils as the wire lays down on the arbor, but you don't want the wire to run over itself as the arbor turns. The gap should look something like this:
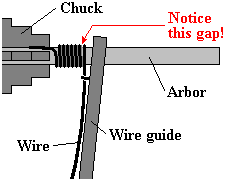
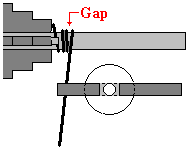
This gap controls what's called "initial tension". Initial tension is the force in the wire that makes it necessary to apply some load to the spring in order to break the coils apart. Garage door springs, for instance, have a LOT of initial tension. Slinky toys (which are basically extension springs without loops) have very little.
Stop winding when the first of these four things happens:
You reach the point beyond which you can't reach the "off" switch on your lathe.
You run out of wire. DON'T LET THE "BACK" END OF THE WIRE PASS THE PIN ON THE WIRE GUIDE!
Your wire guide gets close to the end of your arbor.
(if you're just going to make one spring) If the coils on the arbor measure about 1-1/4 times the length of the body of the spring you're trying to make.
Back off the chuck so that the spring is loose on the arbor. If you're using light wire, you can just grip the body of the spring near the chuck and pull the dogleg out, loosening your grip slowly so that the coils unwind slowly. Slide the wire guide and the spring off the arbor.
Put your spring into the oven and relieve the stress. Remember, springs made of stainless steel wire will open up a little in the heat, while springs made of music wire will contract.
When you've finished this process, let the spring air-cool and check the diameter. If you did your setup properly, it should be just what you want. Then, look at the coils. They should all lie flat against each other, all the way out to the ends of the spring body. If you see gaps in the body of the spring, that means that you let the wire guide go too far to the right while you were coiling.
Now, another word about initial tension. It may or may not be important whether the loops on the ends of your spring line up with each other or cross. If the spring is long enough, you can twist the loops so that they either align or cross, and the initial tension in the coils will hold them in that position.
The information that follows, which will tell you how to make loops, assumes that the position of the loops IS important: if it's not, then just make the loops and let the spring's initial tension take care of how they align.
Making Loops
This section will tell you how to make one type of loop; a basic, no-frills type of loop that will do the trick for most springs. There are other types of loops that are stronger and prettier but to make them, you need tooling that is specially made for making this type of loop and nothing else. Brillisour & Moline used to make looping pliers designed for light wire, but I'm afraid they're out of business.
.
NEWS FLASH: "Hook-Kon" brand looping pliers are available from Advance Car Mover! These are the same pliers mentioned above - I've got a pair and they work great for light wire extension springs!
Simple loops:
Cut off the end of your spring, leaving only coils that touch each other all the way around.
Mount your spring between two looping plates in a vise, like this:
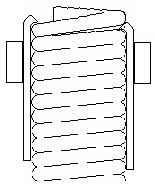
Reach into the center of the spring coil with your looping rod, hooking the tip of the rod under the first coil:
Bend the coil upwards by pushing down on the rod until when you let go, the top of the coil is directly over the center of the spring:
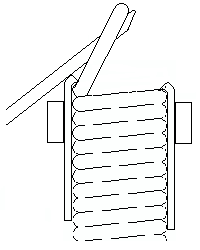
With the looping rod, reach under the coil you just bent up and snag the end of the wire with the tip of the rod:
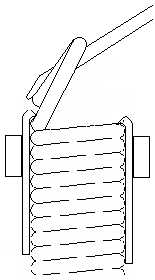
Bend the end of the coil so that it aligns with the body of the spring itself:
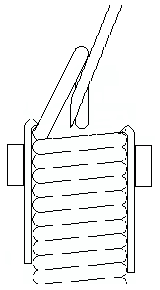
Now you've made one end of the spring. The next thing to do is to figure out how much you have to cut off the other end to make the whole thing the length you want it to be. If it's a matter of being just a little short, you can always extend your hooks by straightening out the wire after if comes off the body of the spring.
If it's a short spring and you're just making one from the coil you have, count the coils and add enough to make the loop - just shy of a full coil.
If it's a short spring and you've wound a long coil, do the same thing and separate the first spring from the main body with wire cutters (or with your cutoff wheel, if you're working with heavier wire). You can cut the whole coil to about the right length, but remember, you have to add "just shy of a full coil" to each end of the spring to make it come out right.
If it's a long spring (or you just don't want to bother counting coils), measure the body of the coil and then add about 1-3/4 coils.
Once you've trimmed the body to size, go ahead and make the second loop, exactly the same way that you made the first. Then, doublecheck the length of the spring - usually, inside one hook to inside the other will give you the best check on this - and see if it's what you want.
If it's too short, you have a couple of options. You can make the next spring with more coils in the body, or you can make the next spring with the fancier type of loop.
Loops and Hooks
Loops will work best for most extension springs. Sometimes, though, you'll want hooks - like when you'll want to slip the spring onto a pin, for instance.
Making hooks is very simple, once you've made loops: all you have to do is cut the end of the wire off so that it doesn't come all the way around to the body of the spring:
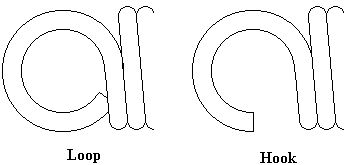
Swivel Hooks
Extension springs are sometimes made with hooks that swivel:
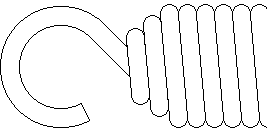
Doing this without kickpress tooling is abysmally difficult, so your best bet, if you have to have this type of spring, is to have it made commercially.
Forward to Finishing.
Terms of Use
|